EYELID FACADE
Location Tehran, Iran
Date 2018
EYELID FACADE
Tehran, Iran | 2018
Designers: NEDA YOUSEFI, MEHRDAD AZIZKHANI
The upper eyelid mechanism of the human eye has been used to make this panel. The eyelid works so that the report of any danger, the entry of dust and moisture into the eye, is transferred to the brain, and then the received information is processed by the brain, and if necessary, the upper eyelid is ordered to close.
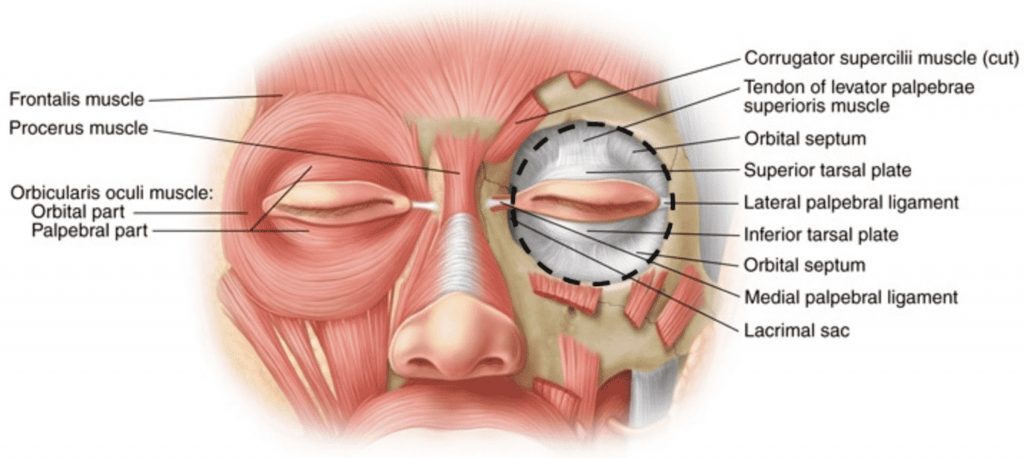
This command is transmitted through a set of nerve fibers called the oculomotor nerve to the levator palpebrae superioris muscle, causing it to open. The upper tarsal plate muscle is attached to the superior tarsal plate. There are also tendons on both sides of the eyelids called medial palpebral ligament and lateral palpebral raphe, which act as elastic and act as support for the eyelids.
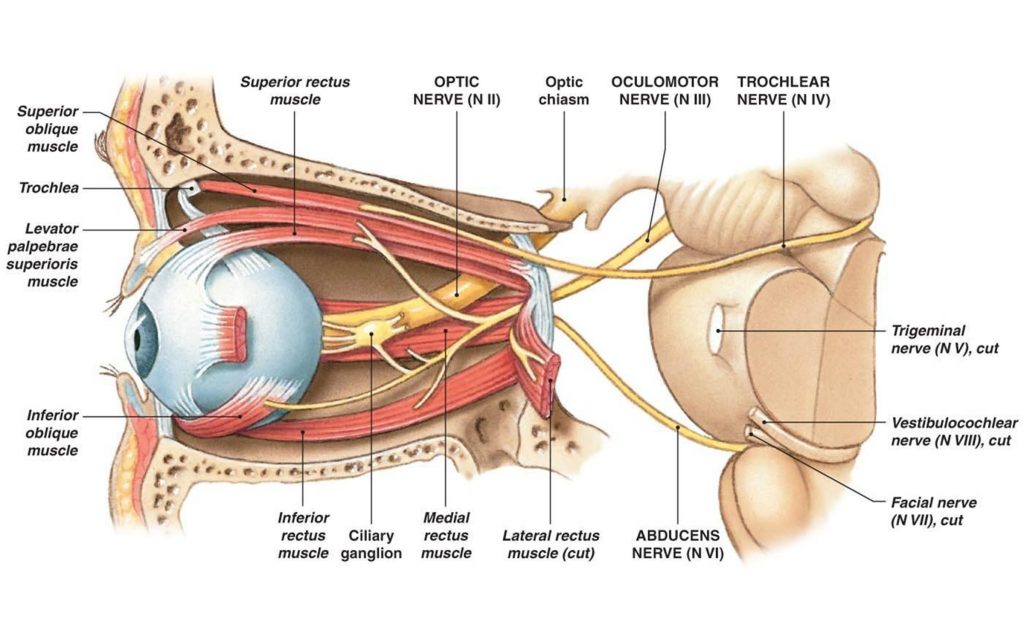
To create a smart panel inspired by the upper eyelid of the human eye, first, the rhombus geometry, the closest geometric shape to the human eye, was selected as the initial module, considering the possibility of repetition on the facade of the building. Then, a special type of fabric that was resilient was selected as the panel covering material. Next, an elastic band was installed as the supporting tendons from the top to the bottom of the rhombus.
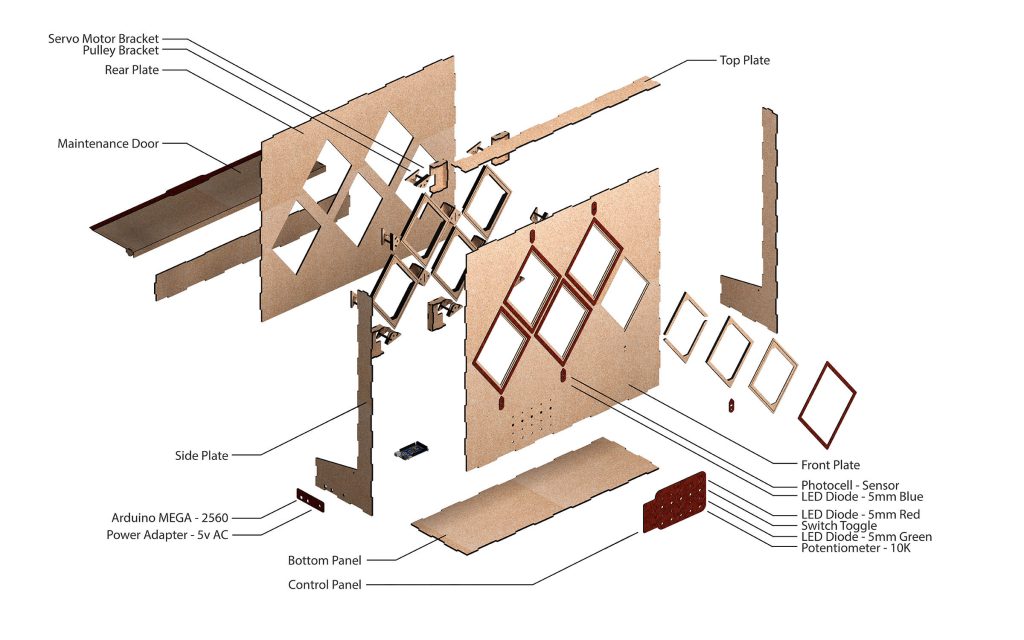
These clamps were connected to a servo motor by strings. The motor in this system plays the role of the levator palpebrae superioris muscle. Environmental information is received by the Photocell sensor from the space around the panel and, like the’s eye’s nervous system, is transmitted to the device’s brain for processing, which is an Arduino MEGA-2560 board. This information goes to the computer via a USB cable and is processed in grasshopper software and then by the FireFly plugin, and the desired command is transmitted to the engine.
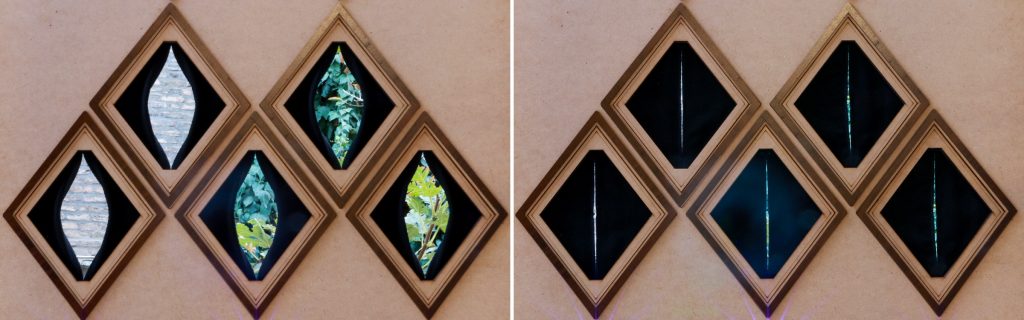
The program of this project was designed in such a way that each panel could separately receive information about light outside the building and information about heat inside the building and then respond to these changes.
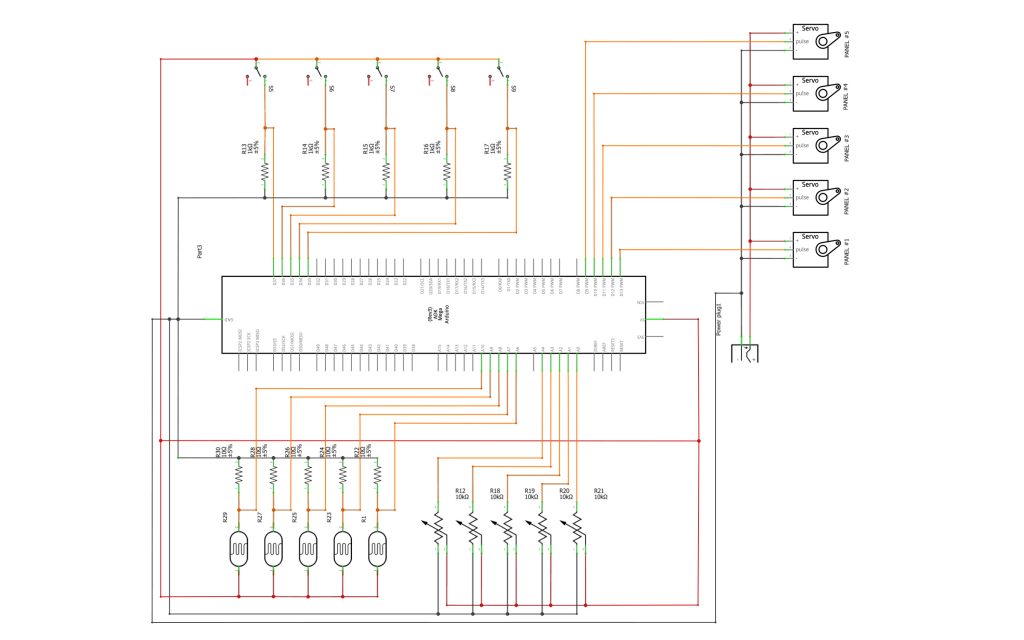
One of the challenges of this project was the ability to change each panel separately, so a switch was installed for each panel so that it could be changed from smart to manual mode, and the amount of open or closed panels could be changed manually. Therefore, each panel can be taken out of smart control and repaired or changed.